CERTAINLY A HIGHER LEVEL OF QUALITY
To ensure a consistently high level of quality, we have our own fully equipped laboratory for complete control of raw materials and final products. Perfect grains and tested raw material quality are necessary to produce the best flour and flour blends.
When the grain is delivered, an automatic sampler is used to take a precisely defined average sample from each delivery. This is then analysed in detail in the company’s laboratory using state-of-the-art analytical equipment. Based on this, each delivery of raw materials is categorised according to quality. This sample is kept as a sealed reference sample for two years to ensure traceability throughout the production chain.
Our Certifications
- IFS / International featured standard
(IFS Food 7 / dated July 2023) - EGM Certificate (European Cereal Monitoring) (Monitoring of hazardous substances Biotask AG)
- Kosher Certificate (Jewish Community of Vienna)
- AMA-Gütesiegel (AMA Quality Seal – the quality label) (Austrian origin)
- BIO Certificates (SLK Salzburg, AMA-Biosiegel (AMA Quality Seal – the bio label))
- Austria Gütezeichen (Austria Quality Seal) (OQA Austrian Society for the Promotion of Quality)
- GVO-frei-Zertifikat (GMO-free Certificate) (SLK Salzburg)
- QS Certificate for milling by-products
Our Certifications
- IFS / International featured standard
(IFS Food 7 / dated July 2023) - EGM Certificate (European Cereal Monitoring) (Monitoring of hazardous substances Biotask AG)
- Kosher Certificate (Jewish Community of Vienna)
- AMA-Gütesiegel (AMA Quality Seal – the quality label) (Austrian origin)
- BIO Certificates (SLK Salzburg, AMA-Biosiegel (AMA Quality Seal – the bio label))
- Austria Gütezeichen (Austria Quality Seal) (OQA Austrian Society for the Promotion of Quality)
- GVO-frei-Zertifikat (GMO-free Certificate) (SLK Salzburg)
- QS Certificate for milling by-products
100 % controlled
Grain by grain
Facts & Figures
- Staff: mill & logistics
65 employees in total - Storage capacity
Grain silo: 15.000 tonnes
Flour and loading silo with 100 cells: 5.000 tonnes
Warehouses (final products): 3.500 tonnes - Milling
Wheat mill: 500 tonnes / day
Rye/spelt mill: 60 tonnes / day - Flour silo
Fully automatic batch mixing system with micro-component dosing system
Capacity: 25.000 kg / h
Flour bagging system for 25/50 kg →
Capacity: 500 bags / h
Flour mixing plant for specialty products → Capacity: 8.000 kg / h. - 3 small packaging systems (fully automatic)
L1: 1 kg system: 6.000 kg / h
L2: 1 kg system: 7.000 kg / h
L3: 5 kg system: 6.000 kg / h - Cartoning system for cardboard trays (fully automatic)
Capacity: 7.000 kg / h - 2 bagging systems for 25-50 kg bags (fully automatic)
Capacity: 15.000 kg / h - 3 palletisers (fully automatic)
Capacity: 30.000 kg / h - Vehicle fleet
16 lorries
10 silo trailers
8 tarpaulin trailers
Facts & Figures
- Staff: mill & logistics
65 employees in total - Storage capacity
Grain silo: 15.000 tonnes
Flour and loading silo with 100 cells: 5.000 tonnes
Warehouses (final products): 3.500 tonnes - Milling
Wheat mill: 500 tonnes / day
Rye/spelt mill: 60 tonnes / day - Flour silo
Fully automatic batch mixing system with micro-component dosing system
Capacity: 25.000 kg / h
Flour bagging system for 25/50 kg →
Capacity: 500 bags / h
Flour mixing plant for specialty products →
Capacity: 8.000 kg / h. - 3 small packaging systems (fully automatic)
L1: 1 kg system: 6.000 kg / h
L2: 1 kg system: 7.000 kg / h
L3: 5 kg system: 6.000 kg / h - Cartoning system for cardboard trays (fully automatic)
Capacity: 7.000 kg / h - 2 bagging systems for 25-50 kg bags (fully automatic)
Capacity: 15.000 kg / h - 3 palletisers (fully automatic)
Capacity: 30.000 kg / h - Vehicle fleet
16 lorries
10 silo trailers
8 tarpaulin trailers
Facts & Figures
- Staff: mill & logistics
65 employees in total - Storage capacity
Grain silo: 15.000 tonnes
Flour and loading silo with 100 cells: 5.000 tonnes
Warehouses (final products): 3.500 tonnes - Milling
Wheat mill: 500 tonnes / day
Rye/spelt mill: 60 tonnes / day - Flour silo
Fully automatic batch mixing system with micro-component dosing system
Capacity: 25.000 kg / h
Flour bagging system for 25/50 kg →
Capacity: 500 bags / h
Flour mixing plant for specialty products →
Capacity: 8.000 kg / h. - 3 small packaging systems (fully automatic)
L1: 1 kg system: 6.000 kg / h
L2: 1 kg system: 7.000 kg / h
L3: 5 kg system: 6.000 kg / h - Cartoning system for cardboard trays (fully automatic)
Capacity: 7.000 kg / h - 2 bagging systems for 25-50 kg bags (fully automatic)
Capacity: 15.000 kg / h - 3 palletisers (fully automatic)
Capacity: 30.000 kg / h - Vehicle fleet
16 lorries
10 silo trailers
8 tarpaulin trailers
A clean affair
OPTIMUM CLEANING IS THE BASIS FOR THE PUREST FLOUR
Haberfellner stands for the purest flour for the finest pastries. This is ensured by optimum cleaning, continuous monitoring of hazardous substances as well as Sortex’s state-of-the-art colour sorter. These high-tech colour sorters use built-in cameras to capture each individual grain and check its surface quality. Damaged grains are automatically detected and removed by air nozzles. Only these machines can completely sort out both the highly toxic ergot and grain contaminated with mould and fusarium toxins* before milling.
*The term fusarium toxins covers a large group of mostly highly toxic metabolic products of phytopathogenic fungi of the genus Fusarium.
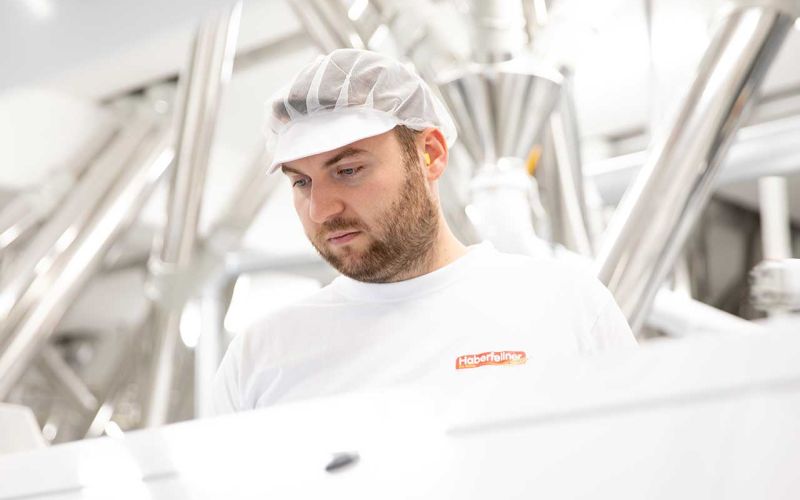
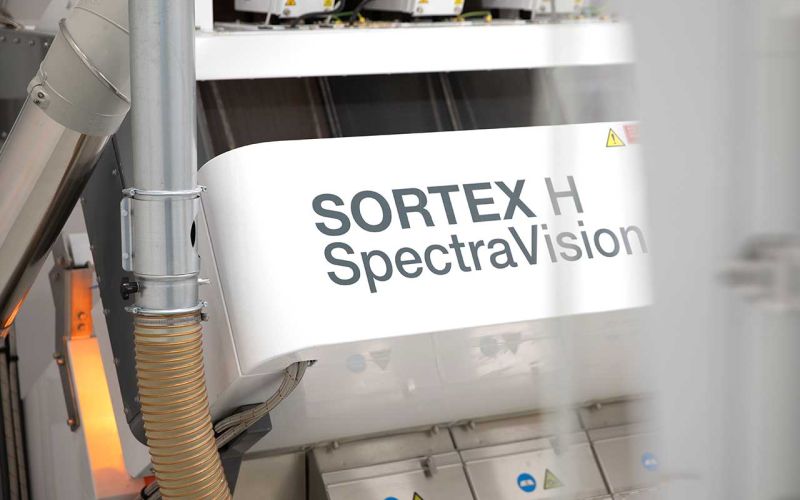
Leading the way with technology
State-of-the-art production technologies
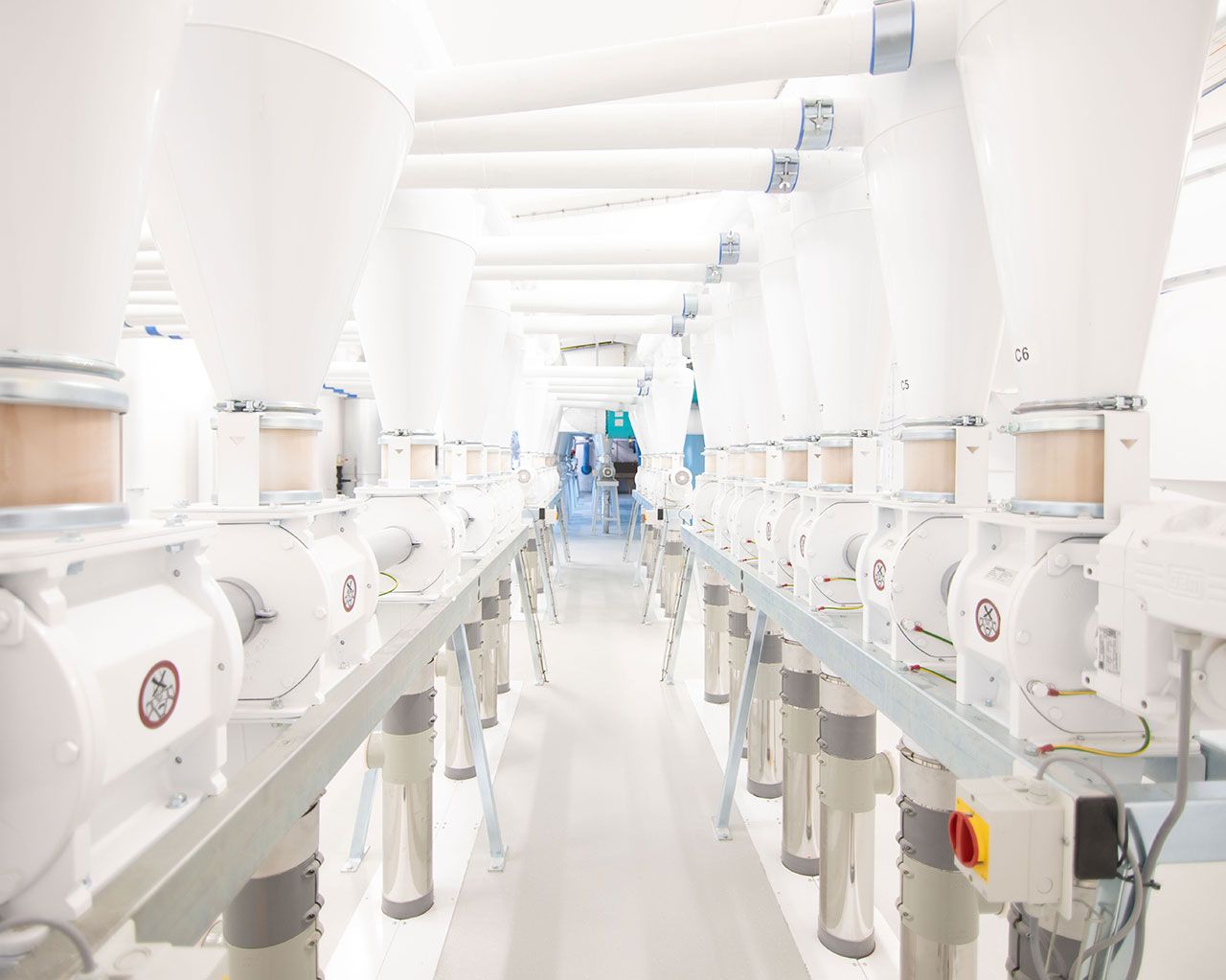
